Design Features and Decisions at University of Iowa Stead Family Children's Hospital
The University of Iowa Stead Family Children’s Hospital is designed as a healing environment to minimize stress, encourage hope, and provide comfort. Every detail has been planned to meet the unique needs of our pediatric patients and families. From the moment visitors step into the lobby, they will see spaces that engage, entertain, and invite discovery.
Here are some of the ways families will benefit from the design decisions throughout our hospital:
Energy Efficient Design
University of Iowa Stead Family Children’s Hospital is LEED Gold certified
What is LEED?
LEED stands for “Leadership in Energy and Environmental Design.” It represents forward thinking, innovative, and time-tested approaches to creating environmentally sustainable buildings that better our world and enhance human health and community.
- LEED is an internationally recognized certification process based on a range of principles that reduce the environmental impact linked to the construction and operation of “green” buildings.
- The aim is to produce a building that is environmentally responsible and uses resources efficiently. LEED uses a points-based system rewarding different levels of sustainability achieved. These levels include Platinum at the highest, followed by Gold, Silver, and Certified.
- Sustainable features of University of Iowa Stead Family Children’s Hospital fall into the following LEED categories:
- Sustainable SitesIn their words
- Water Efficiency
- Energy and Atmosphere
- Materials and Resources
- Indoor Environmental Quality
- Innovation in Design
- Regional Priority
Sustainable Sites
Sustainable sites discourages development on previously undeveloped land; seeks to minimize a building’s impact on ecosystems and waterways; encourages regionally appropriate landscaping; rewards smart transportation choices; controls storm runoff; and promotes reduction or erosion, light pollution, heat island effect, and construction-related pollution.
- University of Iowa Stead Family Children’s Hospital is constructed on previously developed land. This helps protect habitats of endangered species and existing wetlands.
- During the demolition of the previous Parking Ramp 2, excavation of the site, and construction of the new building, the building’s contractors reduced airborne dust generation, soil erosion, and sedimentation into local waterways.
- The site is covered with planted areas which help reduce water runoff and the heat island effect. A white PVC roof and light-colored site paving also reduce the ambient temperature in the summer.
- Access to public transportation and bicycle racks reduce the effects of fossil fuel consumption and emissions from driving personal vehicles.
- Convenient parking is provided which gives preference to low-emitting and fuel-efficient vehicles.
Water Efficiency
Water efficiency encourages smarter use of water. Water reduction is typically achieved through more efficient appliances, fixtures, and fittings inside and water-conscious landscaping outside.
- Water conservation helps save on energy costs, especially for providing hot water as well as pumping water. Efficient water usage reduces University of Iowa Stead Family Children’s Hospital’s water supply costs, maintenance, and life-cycle costs.
- Conservation measures in the building and surrounding community help prevent water shortages.
- The building uses water-efficient plumbing fixtures such as dual flush toilets, aerated sensor faucets on sinks, low-flow shower heads, and low-flow urinals to reduce water usage by 20 to 30 percent less than a comparable building type.
- The site has an efficient water irrigation system and native plants that require less water than other landscape material. These hardier plants also require less or no fertilizers and pesticides that in turn will reduce other environmental degradation.
Energy and Atmosphere
Energy and atmosphere encourages a wide variety of energy-wise strategies: energy-use monitoring; efficient design and construction; efficient appliances, systems, and lighting; the use of renewable and clean sources of energy generated on-site or off-site; and other innovative measures.
- University of Iowa Stead Family Children’s Hospital performs far better than an average baseline building by comparison. This building is designed to function at a high-performance level and commissioned to ensure the systems function as designed.
- Energy efficiency examples include: ample daylighting to reduce lighting needs and costs; well-sealed and insulated exterior walls and roofs; and insulated low-E exterior doors and windows to reduce heating and cooling costs; light-colored roofing to reduce heat gain and reduce cooling costs; state-of-the-art LED light fixtures to reduce electrical costs; and highly efficient HVAC (heating, ventilating, air conditioning) equipment to reduce energy costs.
- Commissioning was done to ensure the building systems and their controls perform as specified. This leads to lower operating costs, improved indoor environmental quality, fewer maintenance issues, and increased occupant comfort and productivity.
Materials and Resources
Materials and resources encourages the selection of sustainably grown, harvested, produced, and transported products and materials. It promotes waste reduction as well as reuse and recycling, and it particularly rewards the reduction of waste at a product’s source.
- During the demolition of the previous Parking Ramp 2 on the future University of Iowa Stead Family Children’s Hospital site, care was taken to send nearly all the debris to be recycled in lieu of sending it to a landfill.
- The building has a robust recycling program. Single-stream recycling and composting is available and dedicated space is included for the collection and storage of waste materials to be recycled.
- The building includes materials and furniture items that are made of recycled content.
- Using regional materials and labor reduces transportation fuel costs and keeps jobs and money in the local economy. The concrete that makes up most of the building’s structure and the adjacent underground parking ramp was manufactured by nearby companies from locally extracted materials.
Indoor Environmental Quality
Indoor environmental quality promotes strategies that improve indoor air quality as well as those that provide increased thermal comfort and better lighting for occupants, and control of the interior environment systems by individuals necessary to maximize occupant comfort and productivity.
- University of Iowa Stead Family Children’s Hospital requirements for indoor air quality by building code are already much greater than for a standard building. Children in general are more sensitive and susceptible to respiratory irritants that will aggravate asthma, especially children who are acutely ill. The building’s outdoor air ventilation system is designed to be at least 30 percent higher than the code minimum.
- Smoking is prohibited everywhere on the University of Iowa Health Care campus, both inside and outside buildings.
- Low-emitting materials are used as the standard for all building products that have been installed inside the building envelope. Low-emitting building products have low VOC’s (volatile organic compounds). This includes all adhesives, sealants, paints, coatings, and all composite wood products such as plywood.
- Individual lighting controls are provided for 90 percent of all occupants. Fifty percent of all individual spaces have access to a thermostat, and shared spaces have access to the thermostat for that shared zone.
Innovation in Design
Innovation in design provides extra points for projects that use innovative technologies and strategies to improve a building’s performance well beyond what is required by other LEED credits, or to account for green building considerations that are not specifically addressed elsewhere in LEED. This category also rewards projects for including LEED Accredited Professionals on the team to ensure a holistic, integrated approach to the design and construction process.
- University of Iowa Stead Family Children’s Hospital minimizes mercury contained in various building devices such as light bulbs and thermostats.
- The building uses a green cleaning program as the standard operating procedure to reduce building occupant’s exposure to chemical, biological, and particulate contaminants.
- One hundred percent of the parking is covered in the attached underground parking ramp with a mostly landscaped site above with light colored paving to create a cooling effect.
- The building uses 70 percent green power.
- An education program on the mission and significance of the LEED certification program and recycling features include a recycling-themed Zen coloring book and a comprehensive signage program explaining the benefits of this sustainable building and recycling guidance.
Regional Priority
Regional priority provides additional points as an incentive for the achievement of existing credits among the various other LEED categories. This category addresses geographically-specific environmental priorities that the U.S. Green Building Council local chapters have determined are of critical importance.
- University of Iowa Stead Family Children’s Hospital is in a location of significant development density and features abundant community connectivity to numerous services that is easily walkable.
- The site has convenient access to public transportation that enables connections throughout Iowa City and neighboring towns while reducing the need for individual automobiles and land dedicated to parking.
- The project includes conveniently located and ample bicycle storage racks nearby as well as shower and changing rooms for bicyclists to promote alternative cleaner transportation and personal fitness.
- Extensive and vigilant recycling efforts in construction waste management during the project enabled a significant amount of construction debris to be diverted away from landfills to help preserve valuable farm land and precious natural ecosystems.
Designing a new hospital created an opportunity to improve efficiency and enhance patient safety. The concept of standardization guided the design of the entire building, including the layout of rooms and units. Consistent design improves the ability of faculty and staff to locate needed equipment and supplies quickly. It also makes it easier for patients, families, and staff to navigate the facility.
On all levels, an oval hallway provides access to patient rooms, which are located along the outside wall. Lounges, vending machines, and restrooms are in the same location on each level.
Patient rooms also have been standardized. Every patient room includes three areas. There is a care team zone, patient zone, and family zone in each room. The layout of patient rooms is the same on all inpatient units, except Level 3. Level 3 is home to the Pediatric Cardiac Intensive Care Unit (PCICU) and Pediatric Intensive Care Unit (PICU). On that level, equipment and patient care needs dictated some modifications to the layout on other floors.
The dedicated family zone gives families space to rest and eat without leaving their child. Having their own space makes it easier for family members to be involved in patient care. Family zones on all inpatient floors are located closest to the windows.
Hallways for staff, medication rooms, nourishment rooms, and holding areas for trash and recycling are also in the same locations on all inpatient floors. The layout of these rooms is the same, enhancing productivity. Standardizing the location and design of medication rooms help reduce the risk for errors, a key factor in patient safety. The familiarity associated with the standard design makes it easier for environmental services (housekeepers), nurses, and other employees to float between levels in an efficient manner.
Nursing played a key role in establishing the need for same-handed rooms, which proved critical in how rooms were designed. Same-handededness means that the layout (where the patient’s bed is located, for example) is identical for rooms on each level. No matter which room the staff enters, they know where to find equipment, sinks, supplies, and computers. Even light switches are in the same place. In emergencies, consistent design allows the care team to focus more on helping patients than finding needed items. Research suggests that same-handed design can help employees reduce errors and improve safety. That’s because the habits learned in one room transfer easily to others.
What does same-handed design mean for patients and families? For patients, it means knowing where to find the TV, light switches, bathrooms, etc., any time they are in the hospital. Bathrooms are inboarded, or located near the entrances in all patient rooms except those in the PCICU/PICU. There, bathrooms are outboarded, or located in the rear of rooms. Every family can be assured of having the same furnishings in the same spot, no matter which room they are assigned on a given level. This includes a refrigerator for family use and a sleeping area large enough for two adults to spend the night comfortably.
The standard design also creates a level of comfort for families who experience frequent admissions. Familiarity helps make the hospital seem more like home. For example, adjusting the thermostat or controlling shades in one room is identical to doing so in any other room.
The standard room design helps environmental services employees clean rooms more efficiently. They no longer need to look around to find trash and soiled linen containers. With a standard procedure for cleaning every room, and continuous seam, integral base rubber flooring, they can also do their jobs more effectively. Clean rooms reduce the potential for infection, enhancing healing.
Consistent design standards are used in other clinical areas. Operating rooms are same-handed in design. No matter which room a surgeon, anesthesiologist, or perioperative nursing team uses, they always know what to expect upon entering. Rooms on the Post-Anesthesia Care Unit (PACU) and the pre/post rooms are same-handed, too.
It’s not only the physical space that are standardized. Employees are also adopting standard procedures to ensure a common approach to work.
Standardization allows teams to ensure the adoption of the highest standards associated with the design of our children’s hospital. And that’s great news for everyone.
Our hospital’s state-of-the-art heating, ventilation, and air conditioning (HVAC) system provides maximum comfort for patients with minimal noise. Every inpatient room has its own thermostat, allowing families to create a climate customized to their needs.
To provide the cleanest air possible, the hospital employs high-efficiency particulate air (HEPA) filtration. HEPA filtration reduces the risk of infection to patients, staff, and visitors. That’s because air on all patient floors are filtered to remove 99.9 percent of pollutants. This includes dust, pollen, mold spores, and bacteria. In addition, operating rooms and rooms for high-risk patients are outfitted with additional filters at the vents.
The HVAC system is massive. Twenty-four air handling units of various sizes circulate air throughout our hospital. Two huge units located on level 12 serve levels 6 through 11. (These include four inpatient floors and two floors for future use.) Remarkably, the two units are the largest ever made by the manufacturer. How big are they? Picture a standard-size volleyball court with an 11-foot ceiling!
These enormous units are equipped with two large fan arrays. Each array consists of several fans, allowing the unit to operate at full capacity even if one fan fails. Large arrays eliminate the need to take the entire unit off-line in the event of a minor mechanical issue.
Despite the large number of fans, the HVAC system is very quiet. This is important because a quieter building creates a better environment for healing. To ensure the system meets our patient and families’ needs, members of the construction team traveled to Oklahoma to test the fan arrays. Their goal was to ensure that the noise generated fell well below a certain level. As it turns out, the fans are so quiet that the tester did not realize they were in use when he first encountered them.
Design Features to Take Notice Of
University of Iowa Stead Family Children’s Hospital includes more than 1,500 pieces of furniture from 21 different manufacturers.
Buying new furniture for a hospital isn’t as simple as walking into a store and picking out a few items. When choosing furniture, we gathered input from a team of employees, patients, and families. Staff from capital management, epidemiology (causes and prevention of diseases), environmental services (housekeeping), and nursing worked on the project.
The team used an evidence-based design (EBD) process. EBD refers to using facts and other types of reliable information to influence design. The overall goals of furniture in the hospital included:
- Providing comfortable accommodations
- Reducing surface contamination linked to health care-related infections
- Preventing or reducing patient falls and related injuries
- Decreasing medication errors
- Improving communication and social support for patients and families
- Decreasing stress and fatigue for patients, families, and staff
- Improving staff effectiveness, efficiency, and communication
- Improving environmental safety
- Representing the best investment
For each goal, key standards were written. For example, to prevent or reduce falls and injuries, the team specified that all rolling furniture include locking rollers or casters. Chairs were required to have armrests, and chair seat height had to be adjustable.
The team selected furniture that would not appear outdated in a few years. It was important to find options that would allow flexibility, too. For example, stacking chairs in public spaces would make it easy to rearrange seating quickly. Ideally, the chairs and tables selected could be moved easily to meet the needs of different-sized groups.
The children’s hospital and John Pappajohn Pavilion (JPP) are connected on seven levels. This design element makes for safe and convenient travel between the two buildings possible.
The connectors on Levels 1 and 2 are open to the public. Connectors on other levels are reserved for faculty and staff and for transporting patients and materials. Access to the connectors on patient care floors may be restricted to employees working on those floors within the children’s hospital. For example, the connector on Level 5 is be restricted to those working in or supporting perioperative services.
All of the connectors keep pedestrians warm in the winter, cool in the summer, and dry year-round. They offer quick and convenient access between buildings. The distance between the children’s hospital and UI Hospitals & Clinics is only 42 feet via the connectors. This reduces travel time, increasing efficiency.
On Level 1, a connector links JPP near Elevator I to the lobby of the children’s hospital. Large windows in the connector let in natural light. The connector also feature a mini-museum. Photos, graphics, and objects tell the history of the children’s hospital since it was founded in 1919. After entering the children’s hospital from the connector, families turn right to reach the information desk and elevators.
From 9 p.m. to 6 a.m., the entrance to the children’s hospital at the end of the connector is closed to the public. Families are still be able to reach the lobby of the children’s hospital without going outside. To do so, they veer right near the end of the connector and follow a glass-enclosed walkway to the main entrance, directly in front of the valet parking drop-off. The main entrance of the children’s hospital is open 24/7, and families need to check in with security at the information desk during overnight hours.
A connector on Level 2 links the entrance of the Pediatric Specialty Clinic in JPP with the retail pharmacy on Level 2 of the children’s hospital. This bridge is open to the public from 6 a.m. to 9 p.m. When it is not open to the public (9 p.m. to 6 a.m.), hospital employees are able to access it using their ID badges.
As part of the construction process, additional space was added in JPP on Levels 3 through 6 adjacent to the connectors. The construction enables the hospital to expand available space for adult and pediatric services. For example, on Level 6, the space allows for construction of three additional Neonatal Intensive Care Unit (NICU) rooms.
Here’s a breakdown of the connectors available only to faculty and employees; ID badges are required for access.
Lower Level 1—Connector from staff (off-stage) areas in JPP to off-stage areas in the children’s hospital. Open to all employees.
Level 3—Connector from area near the Chronic Pain and Breast Imaging Center in JPP to the Pediatric Cardiac Intensive Care Unit/Pediatric Intensive Care Unit (PCICU/PICU) in the children’s hospital. To be used primarily by employees working in the PCICU/PICU.
Level 4—Connector from area near the Heart and Vascular Center in JPP to off-stage areas on the surgery support level in the children’s hospital. Open to all employees.
Level 5—Connector between the main operating room and two new pediatric catheterization labs in JPP and a corridor near operating rooms in the children’s hospital. Restricted to employees working in or supporting perioperative services.
Level 6—Connector between the NICU in JPP and the NICU in the children’s hospital. Restricted to employees working in the NICU.
As you walk into the Gerdin Family Lobby of our children’s hospital, it’s hard to miss the towering art pieces on display. Resembling stacks of alphabet blocks, the colorful sculptures create a whimsical feel in the large space.
Look more closely, and you’ll see that the pieces, known as wind vanes, celebrate the heritage of various Iowa towns and communities. Every aspect of the wind vanes is eye-catching, but it’s the tops you’re likely to notice first.
At the top of each wind vane, a decorative element turns. Each wind vane sports a different element that pays tribute to the state’s farming roots. One features a rooster poised to crow as the sun comes up over the horizon. Another shows a person digging in the dirt, while a meadowlark sings nearby.
Artist Larry Kirkland of Washington, D.C., came up with the idea for the wind vanes and designed them from top to bottom. Larry creates large-scale works of art for airports, hospitals, office buildings, and other facilities nationwide. All six of the prominently displayed wind vanes were made possible by the generous support of Volunteer Services at University of Iowa Hospitals & Clinics.
From the beginning of his work on the wind vanes, Larry wanted to create something big. It was important, he says, to conceive of something larger than a person but smaller than the lobby’s soaring ceiling. The lobby, with its large windows and curved walls, is a sophisticated space. Within that, he wanted to find a way to declare that “this is a space for children,” he says.
Like any artist, Larry also had to understand his audience. Public areas in children’s hospitals are environments for a patient’s “circle of support,” he explains. Patients may not spend much time in these spaces, but family members do. For example, siblings often pass long hours at a hospital when a brother or sister is ill. Creating a space that helps families feel engaged became part of his mission.
The solid part of each wind vane consists of several Corian® cubes stacked atop each other. Corian is a durable, smooth surface often used for countertops.
Each of the six wind vanes features the names of two Iowa communities, displayed vertically. Larry then divided much of the space on the smooth part of the pieces into small squares. Many squares contain colorful graphics that capture unique aspects of the represented communities.
Some highlight a town’s history, while others reflect the presence of nearby natural areas or industries. For example, one square on the section devoted to Le Mars depicts an ice cream cone. The western Iowa town is known as the “ice cream capital of the world.” Pictures of animals help represent Des Moines since it is home to Blank Park Zoo.
Other squares contain bold geometric patterns that catch the eye and help lend a quilt-like look to the pieces. Geography buffs will want to look for several small map silhouettes of Iowa. There is one for every town featured; each town’s location is pinpointed on the silhouettes.
Four wind vanes are located on the north side of the Gerdin Family Lobby. Not far from the children’s theater, they are visible as soon as you come through the main entrance. Two others are located on the south side near the Janice and Bruce Ellig Library.
Adults and children alike will have fun exploring them, picking out pictures, and looking at the map outlines. The 12 featured communities are:
Boone
Boone is home to one of the longest, highest, double-track railroad bridges in the world. The town has a vibrant musical and performance scene. In addition, an annual festival includes a pet and quilt show.
Corydon
Representing south-central Iowa, Corydon was home to Olympian George Saling. He won the gold medal at the 1932 games in Los Angeles in the 110-meter hurdles. The town includes a 58-acre lake.
Des Moines
Des Moines is best known as the state capital and Iowa’s largest city. Visitors and locals are drawn to the city’s Blank Park Zoo and many cultural events. The city also plays host to the state fair and sporting events, including high school tournaments.
Keokuk
Located where the Des Moines River and Mississippi River meet, Keokuk is the state’s southernmost city. It was named after a Sauk Indian chief. The state’s highest temperature was recorded there. On July 20, 1935, the thermometer reached 118 degrees.
Le Mars
Located in northwest Iowa, Le Mars is home to the world’s largest ice cream manufacturing plant under one roof. The name Blue Bunny was chosen in 1935 through a contest; the winner received $25.
Maquoketa
Maquoketa is famous for the nearby Maquoketa Caves State Park. The park has more caves than any state park in Iowa and is a popular recreational spot. Our new hospital will be named University of Iowa Stead Family Children’s Hospital in November 2016, in honor of the generous support of Jerre and Mary Jo Stead, natives of Maquoketa.
Mason City
Mason City was the home of Meredith Willson, who wrote “The Music Man.” The Broadway musical is considered an American classic. The town is also known for its Prairie School architecture. Frank Lloyd Wright designed Mason City’s Historic Park Inn hotel.
New Albin
New Albin is the northernmost city in Iowa. A 12-sided barn, the Reburn Barn, is located there. Built in 1914, it has a feed trough around a central silo for feeding up to 50 cattle at once.
Red Oak
Named for trees located along the nearby Red Oak Creek, Red Oak represents southwestern Iowa. It has a proud military history and had a victory ship, SS Red Oak Victory, named in honor of it.
Sabula
Sabula is the only town of its kind in Iowa. Why? It’s situated on an island. Located on the Mississippi River, it is also the easternmost town in the state.
Story City
Story City, in the geographic center of the state, calls itself “The Heart of Iowa.” Its antique carousel entertains residents and visitors during the summer.
Westfield
Westfield, the westernmost city in Iowa, is located on a bend in the Big Sioux River. Westfield was the hometown of fictional character Jack Smurch, the main character in James Thurber’s The Greatest Man in the World about a pilot who flies around the world.
Art can provide an escape. It can make people think or laugh. It may spark conversations. These are some of the goals of artwork that is displayed throughout our new children’s hospital. Some pieces are whimsical, and many have been selected to invite discovery. Families and visitors may look at a picture and ask each other, “What do you see?” or “What do you think is going on?” The artwork may even lead to storytelling.
The artwork found at UI Stead Family Children’s Hospital was selected with patients, families, and visitors in mind. More than 300 pieces are installed; a small portion have been transferred from existing pediatric areas. Funding for the artwork comes from the Art in State Buildings program, which was made possible by passage of a 1979 state law, known as a percent-for-art law. It requires that a minimum of one-half of 1 percent (.005 percent) of the state’s portion of total construction costs be allocated to artwork. Private donors also helped provide support for some pieces. The artwork in UI Stead Family Children’s Hospital represents the work of more than 60 artists, half of whom are from the Midwest.
In a hospital, art is more than just a pretty picture. It can help the healing process. According to Global Alliance for Arts & Health, “By reducing stress, loneliness, and the perception of pain, the arts improve the patient experience.”
Color and Lighting
A tractor tilling fields. Dragonflies darting along a river’s edge. A bicyclist out for a ride. These are some of the images that come to mind when people think about Iowa, and they are some of the images that will be part of the “Iowa story” inside our hospital. In fact, each level of the hospital will have its own unique color and icon.
Iowa’s farmlands, prairies, woodlands, rivers, and skies are reflected throughout our hospital. These elements not only reflect Iowa’s natural beauty but also help guide families by creating clear travel paths. The colors featured on each level were chosen after careful study of photographs showing habitats throughout the state. The shades of blue, green, purple, and other colors are also soothing and child-friendly. Some reflect colors of specific objects in real life, such as a red barn in the farming scene or blue water in the river scene.
Patients, visitors, and employees will enjoy picking out details from scenes throughout the hospital that feature the icons. Some icons celebrate Iowa’s farming roots. Others represent wildlife that can be found in our state. A bicycle, canoe, and kite symbolize activities that children enjoy. Fittingly, a hot air balloon represents Level 12. These large balloons rise into the sky in much the same way that our children’s hospital does.
Both the icons and colors are used to guide families throughout the hospital. The wall behind each unit clerk desk (on inpatient floors) display that level’s icon. The icons are also be found on signs and elevator buttons.
Paint hues vary throughout each level, providing a visual clue as visitors move through the halls. The colors are the most vibrant near the public entrance to each level. Hues become lighter as visitors approach the west end of the hospital, nearest Kinnick Stadium.
To provide an added sense of discovery, the icon for each level are displayed on a cabinet next to each patient room door. The large icon is made up of many smaller versions of the same icon. For example, on Level 6, a large blue bird is comprised of many smaller blue birds. For extra fun, a few of the smaller blue birds have been replaced with icons from other floors. Visitors will need to look carefully to notice which ones are out of place. The same concept was used to develop graphics on other inpatient floors.
Examples of the floor icons:
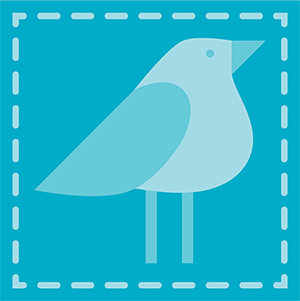
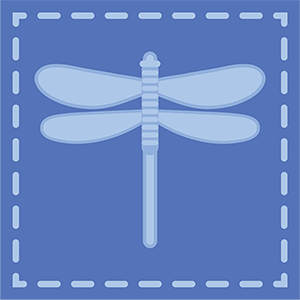
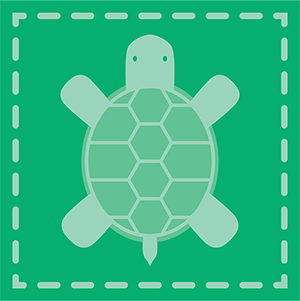
Every aspect of University of Iowa Stead Family Children’s Hospital has been planned to enhance healing and best meet the needs of our patients and families. The paint colors and types of lights found in our hospital are no exception.
Early on, patients and families were asked how the interior of the hospital should be designed. “No white or beige walls” was a popular response. Families wanted an environment that was more welcoming.
Designers selected colors that are known to promote healing. All of the scenes selected reflect Iowa’s natural landscapes of farmlands, prairies, woodlands, rivers, and skies. After studying photographs of our state, designers picked paint colors that echo those found in nature and hues that would contribute to a calming and healing atmosphere.
Picking paint colors was just one aspect of interior design. Dozens of decisions had to be made about the best type of lighting to incorporate throughout the building. The lights not only need to look visually appealing but also need to be energy-efficient, require minimal maintenance, enhance healing, and boost workplace efficiencies.
Here are some of the interesting lighting features in our hospital:
Hallways
Elevator lobbies: Lights in elevator lobbies on each floor matches the color of that floor’s icon. For example, a green fox represents the PCICU and PICU, so lights in the elevator lobby on that floor will be green to aid wayfinding.
Unit clerk desk: A large version of the icon representing that level appears on the front of each unit clerk’s desk. At night, the icons light up, aiding navigation and providing a fun distraction.
Care team stations: At night, blue uplights over each care team station on inpatient floors are turned on. Blue lights have been shown to help keep people awake and alert.
Hallways: At night, lights in hallways on inpatient floors are dimmer than they are during daytime hours. The change in brightness enhances rest and serve as a visual reminder of quiet time.
Other Spaces
Lobby: The welcoming lobby includes large, distinctive globe lights. Recessed lighting helps highlight the “Blooming Wall,” the unique artwork on the interior walls of the Gerdin Family Lobby.
Entrance canopy: Three concentric rings of lights provide needed light while creating a warm and distinctive look for the canopy over the entrance to the hospital.
Lower Level 2: Fiber-optic lights in the ceilings of rooms on Lower Level 2 provides a distraction for patients undergoing imaging or other procedures.
Throughout Hospital
Light wells: Several light wells are located around the perimeter of the hospital. These vertical shafts, extending from Levels 3 to 11, let natural light into nearby spaces, including conference rooms. At night, the light wells are illuminated with a number of different colors, including unique color combinations for holidays and special events.
Designed to Improve the Medical Experience
Our employees want every patient to experience the best possible outcomes. This wouldn’t happen without the knowledge, compassion, and dedication of our entire care team. But healing and good health require more than expert care. Finding ways to reduce the risk of infection is essential, too.
Enter the architects, planners, and construction team for our new hospital. They have taken steps big and small to ensure that our new hospital meets the highest standards for safety. Some of these steps will be noticeable to patients and families. Others will be invisible. Either way, careful planning will help curb the risk of infection and spread of germs, helping our patients heal.
Your private room
In our hospital, every patient has a private room. Single rooms provide more privacy and enhance rest. They also help reduce the spread of germs because patients will not be in close quarters with other patients, families, or visitors.
Maintaining the quality of indoor air is also critical to the health of patients, families, and staff. That’s why our hospital features a high-efficiency particulate air filtration (HEPA) system. The HEPA system will filter out 99.9 percent of contaminants on patient floors. This includes tiny dust particles, mold spores, pollen, and bacteria. All operating rooms and rooms for high-risk patients are equipped with additional HEPA filters at the vents.
Certain rooms are designed with special airflow systems for an added layer of protection. For critically ill patients, air will flow in such a way that germs from the hallway will not be able to enter the patient’s room. In the case of patients with infectious diseases, the air is directed so that it does not reach the hallway. Some of these rooms feature a small anteroom, or buffer room, between the hallway and patient room. Everyone entering and leaving the patient room must pass through the buffer room first. Anterooms allow the proper air pressure to be maintained in both the patient’s room and nearby hallways.
Cabinets, Flooring, and Sinks
Cabinets, flooring, and other elements in each patient room have been carefully selected to help prevent infection. For example, the design of a sink can play a key role in infection prevention. With this in mind, the faucet of each sink in the care team zone is activated by an automatic sensor. As a result, care team members do not need to touch any surfaces to turn the water on and off.
For added safety, the faucet is offset slightly from the drain. This design prevents liquids from around the drain from splashing up when the faucet is turned on. An angled spout also helps to prevent splashing. So does a curved ridge above the basin, along the front of the sink. Cutting back on splashing helps combat the spread of germs.
Standardizing the placement of sinks and gloves in each room also help with infection control. Members of the care team will not need to search for sinks when they walk into rooms. A cabinet outside each patient room door holds personal protection equipment (PPE). Currently, PPE must be stored on carts or in bins that must be moved from place to place.
The children’s hospital features sinks inside the entrance of all inpatient units. Visitors will have a convenient, visible place to wash their hands and/or use hand sanitizer before entering a child’s room. Currently, hand hygiene stations with hand sanitizer are available to visitors in most patient care areas.
The type of flooring used in patient rooms makes cleaning easier. A continuous seam, integral base rubber flooring was selected. Integral base means that the flooring continues up the wall for a few inches. This allows the housekeeping staff to clean the entire floor easily without worrying about a tiny space between the flooring and walls. The continuous seam feature helps prevent infection, too. Without seams or joints, dirty water has no place to hide. A cleaner room means a safer room for everyone.
To make rooms easier to clean, sinks, counters, and other workspaces in the care team zone do not touch the floors. Furniture in the family zone can be moved easily for cleaning. Surfaces of furniture and cabinets are smooth, making them easier to clean than ones with seams or grooves. In bathrooms, trench drains are installed to help drain water efficiently, preventing it from pooling.
Another special feature has been added for the benefit of pediatric cancer patients. Our hospital features two classrooms. The classroom in the University of Iowa Dance Marathon Pediatric Cancer Center serve pediatric cancer patients only, helping to limit their exposure to germs.
The care that went into the selection of these features and others makes our children’s hospital a safer place for patients, visitors, and employees.
In our children's hospital, families and visitors won’t share elevators with food carts. Care team members do not share an elevator with other visitors when transporting patients. That’s because our hospital features two types of spaces: onstage and offstage. Onstage refers to spaces used by the public. Offstage areas are behind-the-scenes spaces limited to use by employees or patients/families escorted by an employee.
On most floors, onstage areas are located along the outer ring of our oval building. These include public elevators, lounges, main hallways, and patient rooms. In the center, or inner core, are spaces designed for employee functions. These include offices, break rooms, and patient and service elevators. The concept of onstage and offstage is based on a model Disney developed for its theme parks. Leading hospitals have adopted this model to increase efficiencies and offer a better healing environment. This concept also guided the design of University of Iowa Health Care—Iowa River Landing, which opened in October 2012.
The onstage/offstage model offers many advantages.
Better patient privacy: Care teams will use offstage patient elevators for moving patients. This will allow patients to be transported between floors efficiently while enhancing their privacy. Also, delivery of supplies and materials will take place using offstage service elevators. As a result, fewer people will walk past patient rooms, enhancing privacy.
Quieter environment: Delivery of medicine, supplies, and equipment will be done mainly offstage. Trash, soiled linen, recycling, and food trays will be stored offstage. Employees will use service elevators to move these items between floors. Fewer rolling carts in hallways means a lower noise level. Care team members will hold huddles offstage, not in hallways outside patient rooms. The pneumatic tube system also will be behind the scenes. Patients will rest more easily since they will be less likely to hear doors to supply rooms or lounges opening and closing.
Better infection control: Offstage elevators will limit patients’ exposure to potential infection risks. How? Patients won’t be exposed as often to members of the public. Patients and families won’t share elevators with trash or soiled linen carts, either. This separation decreases the risk of potential infection.
More open hallways: Offstage storage will cut down on items in hallways. Clearer hallways will offer a more home-like feel. Hallways with fewer carts will be easier for parents and families to navigate.
Faster food deliveries: Service elevators in our hospital will allow staff to deliver food more quickly. Speedier delivery means food should arrive at its desired temperature. That’s a recipe for happier patients and families.
Reduction in food aromas: The smell of food can make some patients nauseated. Young children who see a food cart may not understand why they aren’t allowed to eat before a procedure. Service elevators will help limit exposure to these sights and smells.
Less crowded public elevators: Offstage service elevators will help free up space in elevators used by the public. Offstage patient elevators will also reduce traffic in public elevators.
Increased efficiency: Offstage hallways and elevators will help employees get from place to place more quickly. Many work areas for the care team are offstage, too, further boosting productivity.
Better collaboration: Talking and relaxing behind the scenes can facilitate communication among coworkers. Spaces designed for all care team members to gather on a floor should make working together even more enjoyable.
Hospital employees and families rely on signs outside patient rooms to provide critical information. Some are isolation signs, designed to convey the level of precaution needed to prevent the spread of infection. Others indicate whether a patient has a latex allergy or may be at risk for falling.
In our current hospital, many of these signs are made by the care team and taped to a patient’s room door or adjacent wall. Their placement or appearance is not standardized, varying from floor to floor, even from room to room. In our hospital, there will be one standard sign with universal symbols.
Standardized signs have several advantages. Since care team members always know where to look for the information they need, standardized signs save employees time. Minimal training is needed, even when employees work on more than one floor. As an added bonus, employees no longer need to spend time making signs. Standardized signs also can help ensure compliance by both visitors and employees when it comes to hand-washing and other precautions. In turn, safety for everyone is enhanced.
Finding the right solution involved teamwork among doctors, nurses, and other staff members. Recognizing that standardization was critical, employees also wanted the ability to customize signs to meet the needs of our families and employees.
Each new isolation sign is 8½ x 15 inches. The top of each sign has a header, or horizontal bar, that matches the color of that level in our hospital. Displayed in the header will be the room number in text and Braille representation. Below the header is a space for displaying the patient’s name. The rest of the front of the sign contains a large clear acrylic area. Behind the clear panel, members of the care team will display isolation warning signs as needed. The isolation signage will be the same for every level in our hospital.
But the clear display space is only one integral component of the sign system. The front acrylic panel is hinged. When it is pulled forward and downward, the space inside reveals 10 sliding tabs. Each tab slides horizontally, revealing a smaller sign. The small signs measure about 2 inches by 2 inches; each one is a different color matching the corresponding level in the hospital. Each tab also displays a unique icon representing a different need, request, or warning. For example, one tab displays a food tray overlapped with the universal “no” symbol for prohibition. This tells the food and nutrition staff that the food tray should be delivered to the nurses’ station instead of to the patient. These signs can be scanned quickly, and they’re easy for non-native speakers to understand.
Custom graphics were incorporated on some tabs. For example, a picture of Perky, our children’s hospital mascot, tells the care team that extra comfort is needed, which may mean getting help from a child life specialist. Members of the care team can display as many tabs as needed to reflect the patient’s condition. The entire sign is easy to clean for infection control.
Our innovative signs are colorful and easy to read. More importantly, they will save time and help keep our patients safe.